Hybrid Installation
New Braunfels, TX, January 4, 2023
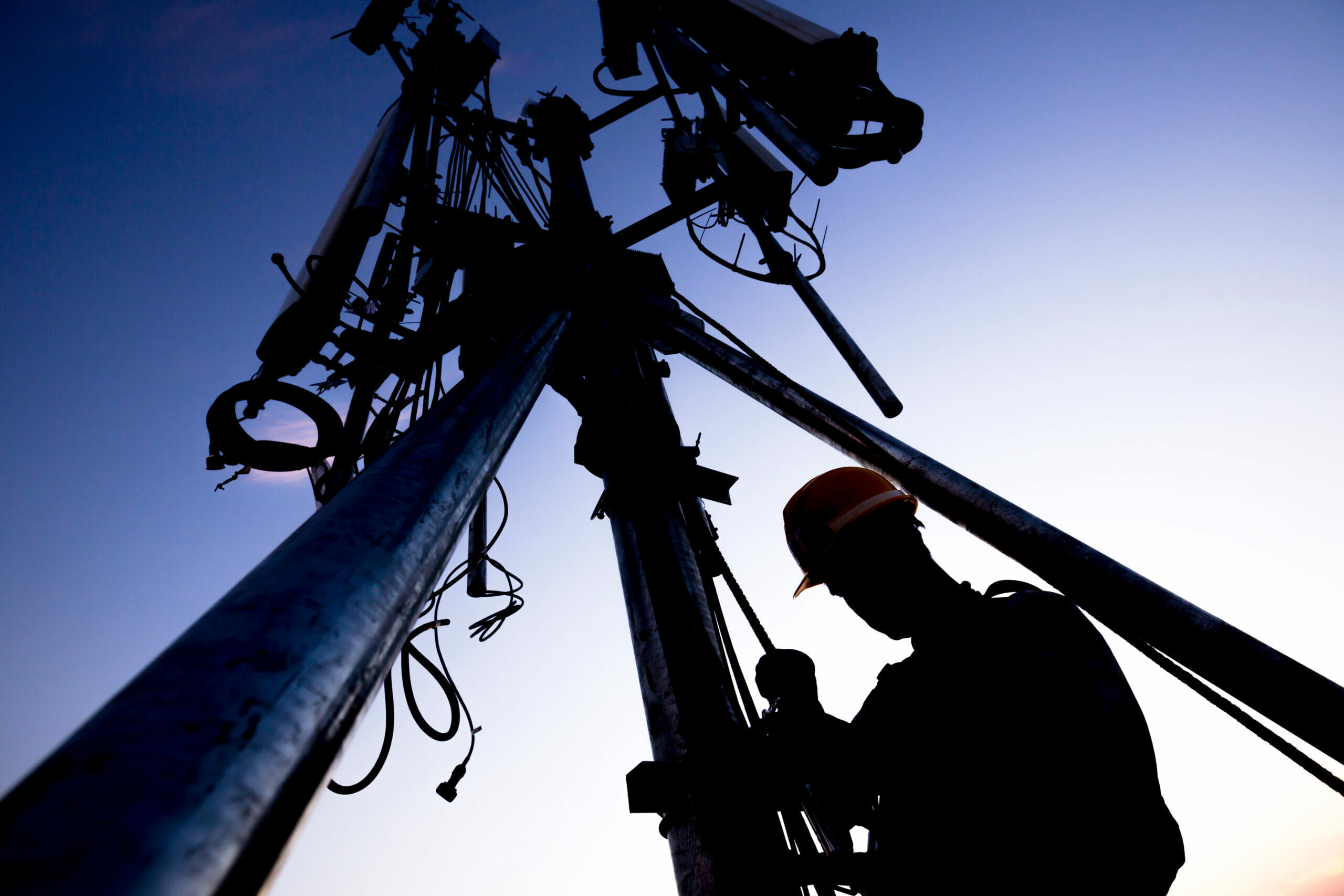
Our industry suffered a tragic loss on December 15th. While the incident is still under investigation, the root cause appears to be related to a failed hoisting grip. We discussed the topic back in November but we thought it important to come back to this subject. The three key points from our previous discussion were to always to secure the hoisting grip, install additional hoisting grips every 200 feet and when possible and support the line back to the structure prior to derigging. Today, we will reinforce one of those key points and discuss a couple of new ones.
- Never raise or lower a hybrid via the hoisting grip
- Inspect hoisting grips prior to loading
- When possible, support the hybrid to the structure prior to derigging
Never raise or lower a hybrid via the hoisting grip without a secondary safety
Hoisting grips are one of the worst-named items in our industry that is used on a regular basis. The practice of using hoisting grips to raise or lower cables has time and time again proven to be dangerous. When lifting or raising cables, a combination of properly rated slings, shackles, and other rigging components must be the method of choice to bear the weight of the cable. Some cables can weigh in excess of 4 lbs. per foot and putting static forces solely on a hoisting grip just isn’t the right thing to do.
Inspect hoisting grips prior to loading
In recent months, we have started to see hybrid cables delivered with hoisting grips pre-installed by the manufacturer. Simply put, we just can’t trust that the grips are good to go. You should always inspect these grips for proper installation and good quality before you actually fly the cable. Keep in mind that someone in a warehouse who might be new on the job, having a bad day, or maybe just isn’t good at it could have installed those grips. Now you’re probably thinking that the manufacturer’s QC process should catch errors but isn’t another look and a couple minutes worth your safety? This extra step is a good one for any item that comes pre-installed from the manufacturer.
When possible, support the hybrid to the structure prior to derigging
There is no doubt that it is best practice to secure a certain percentage of the line back to the structure (i.e., waveguide) prior to derigging the line. This is a failsafe or redundancy in the event something unexpected happens. For coax lines, the general rule of thumb is to support 30% and for hybrid lines, the general rule is to support 75%. Once again, this is best practice. In the event you have bad weather move in, you don’t have to worry about the lines injuring someone, striking the tower, becoming dislodged or getting damaged.
The combination of using properly rated rigging equipment, taking our time, securing cables before derigging, and double-checking our work will lower the chances of something awful occurring on one of our projects. A few months ago, the Ontivity safety and training teams developed a method of procedure that utilizes industry best practices for crews assigned the task of decommissioning or installing new lines on a tower. If you would like more information on this method please reach out to the Ontivity safety team at safety@ontivity.com. Safety is our core value, and we always choose our safety over production. The extra time it takes to do the job right ensures you go home at the end of the day the same way you left in the morning.
If you want more information on those topics, reach out to the Ontivity safety team at safety@ontivity.com, and we will get you taken care of.